Women's Proteus II 3mm
Couldn't load pickup availability
Proteus II Wetsuit 3mm – Unmatched Warmth & Performance✔
✔ Eco-friendly limestone neoprene | ✔ Hexcore & Thermoflex lining | ✔ Semi-dry seal system
The Proteus II 3mm is the warmest and most advanced dive wetsuit in its class. Designed to deliver superior thermal performance with minimal bulk, this suit sets the benchmark for 3mm wetsuits—outperforming many 5mm suits while offering greater flexibility and less buoyancy.
Crafted with greener limestone neoprene, Eco Carbon Black (made from recycled rubber tyres), and water-based Aqua-X glues, the Proteus II significantly reduces CO₂ emissions and eliminates harmful substances in its construction—making it a more eco-conscious choice for divers.
Featuring the renowned Hydrolock neck seal, Glideskin wrist seals, and internal PU ankle seals, this wetsuit is built to minimize water ingress and deliver a semi-dry diving experience. Double glued, blind-stitched, and taped seams further enhance insulation, while Hexcore lining across the torso ensures core warmth during prolonged dives. Thermoflex lining throughout the rest of the suit adds to the overall thermal efficiency.
Collapsible tab content
FOURTH ELEMENT MEN SIZE CHART
Sizes |
Height | Chest | Waist | Inside Legs | ||||
CM | INCHES | CM | INCHES | CM | INCHES | CM | INCHES | |
XS Short | 161 - 169 | 63 - 66 | 76 - 86 | 30 - 34 | 58 - 68 | 23 - 27 | 73 - 77 | 29 - 31 |
XS | 165 - 173 | 65 - 68 | 76 - 86 | 30 - 34 | 58 - 68 | 23 - 27 | 76 - 80 | 30 - 32 |
S Short | 165 - 173 | 65 - 68 | 86 - 96 | 34 - 38 | 68 - 78 | 27 - 31 | 76 - 80 | 30 - 32 |
S | 170 - 178 | 67 - 70 | 86 - 96 | 34 - 38 | 68 - 78 | 27 - 31 | 79 - 83 | 31 - 33 |
S Tall | 176 - 183 | 69 - 72 | 86 - 96 | 34 - 38 | 68 - 78 | 27 - 31 | 82 - 86 | 33 - 34 |
M Short | 170 - 178 | 67 - 70 | 96 - 106 | 38 - 42 | 78 - 88 | 31 - 35 | 79 - 83 | 31 - 33 |
M | 176 - 183 | 69 - 72 | 96 - 106 | 38 - 42 | 78 - 88 | 31 - 35 | 82 - 86 | 33 - 34 |
M Tall | 181 - 188 | 71 - 74 | 96 - 106 | 38 - 42 | 78 - 88 | 31 - 35 | 85 - 89 | 34 - 35 |
L Short | 176 - 183 | 69 - 72 | 106 - 116 | 42 - 46 | 88 - 98 | 35 - 39 | 82 - 86 | 33 - 34 |
L | 181 - 188 | 71 - 74 | 106 - 116 | 42 - 46 | 88 - 98 | 35 - 39 | 85 - 89 | 34 - 35 |
L Tall | 186 - 193 | 73 - 76 | 106 - 116 | 42 - 46 | 88 - 98 | 35 - 39 | 88 - 92 | 35 - 36 |
XL Short | 181 - 188 | 71 - 74 | 116 - 126 | 46 - 50 | 98 - 108 | 39 - 43 | 85 - 89 | 34 - 35 |
XL | 186 - 193 | 73 - 76 | 116 - 126 | 46 - 50 | 98 - 108 | 39 - 43 | 88 - 92 | 35 - 36 |
XL Tall | 191 - 198 | 75 - 78 | 116 - 126 | 46 - 50 | 98 - 108 | 39 - 43 | 91 - 95 | 36 - 38 |
XXL Short | 186 - 193 | 73 - 76 | 126 - 136 | 50 - 54 | 108 - 118 | 43 - 47 | 88 - 92 | 35 - 36 |
XXL | 191 - 198 | 75 - 78 | 126 - 136 | 50 - 54 | 108 - 118 | 43 - 47 | 91 - 95 | 36 - 38 |
XXXL Short | 191 - 198 | 75 - 78 | 136 - 146 | 54 - 58 | 118 - 128 | 47 - 51 | 91 - 95 | 36 - 38 |
XXXL | 196 - 203 | 77 - 80 | 136 - 146 | 54 - 58 | 118 - 128 | 47 - 51 | 94 - 98 | 37 - 39 |
FOURTH ELEMENT WOMEN SIZE CHART
Universal | Height | Chest | Waist | Hips | Inside Legs | |||||
CM | INCHES | CM | INCHES | CM | INCHES | CM | INCHES | CM | INCHES | |
XXS Short | 158 - 166 | 62 - 65 | 68 - 76 | 27 - 30 | 51 - 59 | 20 - 23 | 76 - 84 | 30 - 33 | 69 - 73 | 27 - 29 |
XXS | 160 - 168 | 63 - 66 | 68 - 76 | 27 - 30 | 51 - 59 | 20 - 23 | 76 - 84 | 30 - 33 | 71 - 75 | 28 - 30 |
XS Short | 160 - 168 | 63 - 66 | 74 - 82 | 29 - 33 | 57 - 65 | 23 - 26 | 82 - 90 | 33 - 36 | 71 - 75 | 28 - 30 |
XS | 163 - 170 | 64 - 67 | 74 - 82 | 29 - 33 | 57 - 65 | 23 - 26 | 82 - 90 | 33 - 36 | 73 - 77 | 29 - 31 |
S Short | 163 - 170 | 64 - 67 | 80 - 88 | 32 - 35 | 63 - 71 | 25 - 28 | 88 - 96 | 35 - 38 | 73 - 77 | 29 - 31 |
S | 165 - 173 | 65 - 68 | 80 - 88 | 32 - 35 | 63 - 71 | 25 - 28 | 88 - 96 | 35 - 38 | 75 - 79 | 30 - 31 |
M Short | 165 - 173 | 65 - 68 | 86 - 94 | 34 - 37 | 69 - 77 | 27 - 31 | 94 - 102 | 37 - 40 | 75 - 79 | 30 - 31 |
M | 168 - 175 | 66 - 69 | 86 - 94 | 34 - 37 | 69 - 77 | 27 - 31 | 94 - 102 | 37 - 40 | 77 - 81 | 31 - 32 |
M/L | 168 - 175 | 66 - 69 | 86 - 94 | 34 - 37 | 75 - 83 | 30 - 33 | 100 - 108 | 40 - 43 | 77 - 81 | 31 - 32 |
L Short | 168 - 175 | 66 - 69 | 92 - 100 | 36 - 40 | 75 - 83 | 30 - 33 | 100 - 108 | 40 - 43 | 77 - 81 | 31 - 32 |
L | 170 - 178 | 67 - 70 | 92 - 100 | 36 - 40 | 75 - 83 | 30 - 33 | 100 - 108 | 40 - 43 | 79 - 83 | 31 - 33 |
XL Short | 170 - 178 | 67 - 70 | 98 - 106 | 39 - 42 | 81 - 89 | 32 - 35 | 106 - 114 | 42 - 45 | 79 - 83 | 31 - 33 |
XL | 173 - 180 | 68 - 71 | 98 - 106 | 39 - 42 | 81 - 89 | 32 - 35 | 106 - 114 | 42 - 45 | 81 - 85 | 32 - 34 |
XXL Short | 170 - 178 | 67 - 70 | 104 - 112 | 44 - 44 | 87 - 95 | 35 - 38 | 112 - 120 | 44 - 47 | 79 - 83 | 31 - 33 |
XXL | 173 - 180 | 68 - 71 | 104 - 112 | 41 - 44 | 87 - 95 | 35 - 38 | 112 - 120 | 44 - 47 | 81 - 85 | 32 - 34 |
XXXL Short | 170 - 178 | 67 - 70 | 110 - 118 | 44 - 47 | 93 - 101 | 37 - 40 | 118 - 126 | 47 - 50 | 79 - 83 | 31 - 33 |
XXXL | 173 - 180 | 68 - 71 | 110 - 118 | 44 - 47 | 93 - 101 | 37 - 40 | 118 - 126 | 47 - 50 | 81 - 85 | 32 - 34 |
PONCHOS
Size (Unisex) | Womens UK | Womens US | Height | Chest | ||
CM | INCHES | CM | INCHES | |||
XXS | 6 | 4 | 147 - 160 | 58 - 63 | 56 - 71 | 22 - 28 |
XS | 8 | 6 | 155 - 168 | 61 - 66 | 69 - 84 | 27 - 33 |
S | 10/12 | 08/10 | 163 - 175 | 64 - 69 | 81 - 97 | 32 - 38 |
M | 14/16 | 12/14 | 170 - 183 | 67 - 72 | 94 - 109 | 37 - 43 |
L | 18/20 | 16/18 | 178 - 191 | 70 - 75 | 107 - 122 | 42 - 48 |
XL | 22 | 20 | 185 - 198 | 71 - 78 | 119 - 135 | 47 - 53 |
FOOTWEAR & BOOTS
XS | S | S | M | M | L | L | XL | XXL | XXL | |
UK | 4 | 5 | 6 | 7 | 8 | 9 | 10 | 11 | 12 | 13 |
US | 5 | 6 | 7 | 8 | 9 | 10 | 11 | 12 | 13 | 14 |
EU | 37 | 38 | 39.5 | 41 | 42 | 43 | 44.5 | 46 | 47 | 48 |
HEATWEAR
Size | Head circumference | |
CM | INCHES | |
M | 53 - 59 | 21 - 23 |
L | 56 - 61 | 22 - 24 |
XL | 59 - 64 | 23 - 25 |
HOODS
Size | Head circumference | |
CM | INCHES | |
XS | 48 - 51 | 19 - 20 |
S | 51 - 53 | 20 - 21 |
M | 53 - 56 | 21 - 22 |
L | 56 - 59 | 22 - 23 |
XL | 59 - 61 | 23 - 24 |
XXL | 61 - 64 | 24 - 25 |
GLOVES
Size | Palm circumference | |
CM | INCHES | |
XS | 17 - 19 | 7 - 8 |
S | 19 - 21 | 8 - 8 |
M | 21 - 23 | 8 - 9 |
L | 23 - 25 | 9 - 10 |
XL | 25 - 27 | 10 - 11 |
XXL | 27 - 29 | 11 - 12 |
Fourth Element wetsuits
Combining super thermal Hexcore lining with an innovative double neck seal, the Proteus II is our highest performing dive wetsuit and the choice of many dive professionals around the world. Made from a more eco friendly limestone neoprene using recycled car tyres and water based glues, not compromising on performance.
Features
Proteus II - extra warm
Hydrolock neck system
A second, over-head closure to minimise water ingress.
Taped seams
As well as being glued and stitched, taping ensures seals are waterproof.
Glideskin wrist seals
Create a barrier at the wrist to prevent water entering.
Hexcore torso lining
Plush lining on the core for prolonged water exposure.
Recycled Rubber
One of the key ingredients of neoprene, Eco Carbon Black, is recycled by our wetsuit factory from post-consumer scrap tyres. This significantly reduces energy consumption and cuts CO2 emissions by 200g per wetsuit.
Limestone Neoprene
During the neoprene production process, limestone is used to replace petrochemicals to form rubber chips. You achieve the same performance as traditional neoprene, but with way less environmental impact.
Resources
After the neoprene creation process, the redundant trimmed materials will be recycled and reused in the mixing process to produce more neoprene sheets. Overall huge amounts of raw materials are saved, energy consumption is reduced and waste water and air emissions are minimised during production.
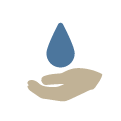
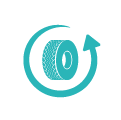
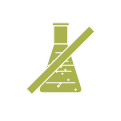
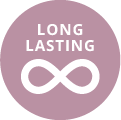